∙ remove ∙ recover ∙ reuse ∙ refine ∙
► Convert 100% of pig and cattle slurry & digestate waste into solid manure, clean permeate water & bio-fertilizer.
► Removes harmful greenhouse gases and water pollutants.
► Advanced modular engineering to integrate with existing facilities.
► Patented & proprietary nutrient recovery technologies.
► Volumes from 20m3 a day.
► Compliant with EU Agricultural Directives and European Green Deal goals.
► Improved farm biosecurity through pathogen removal.
Combined Solutions
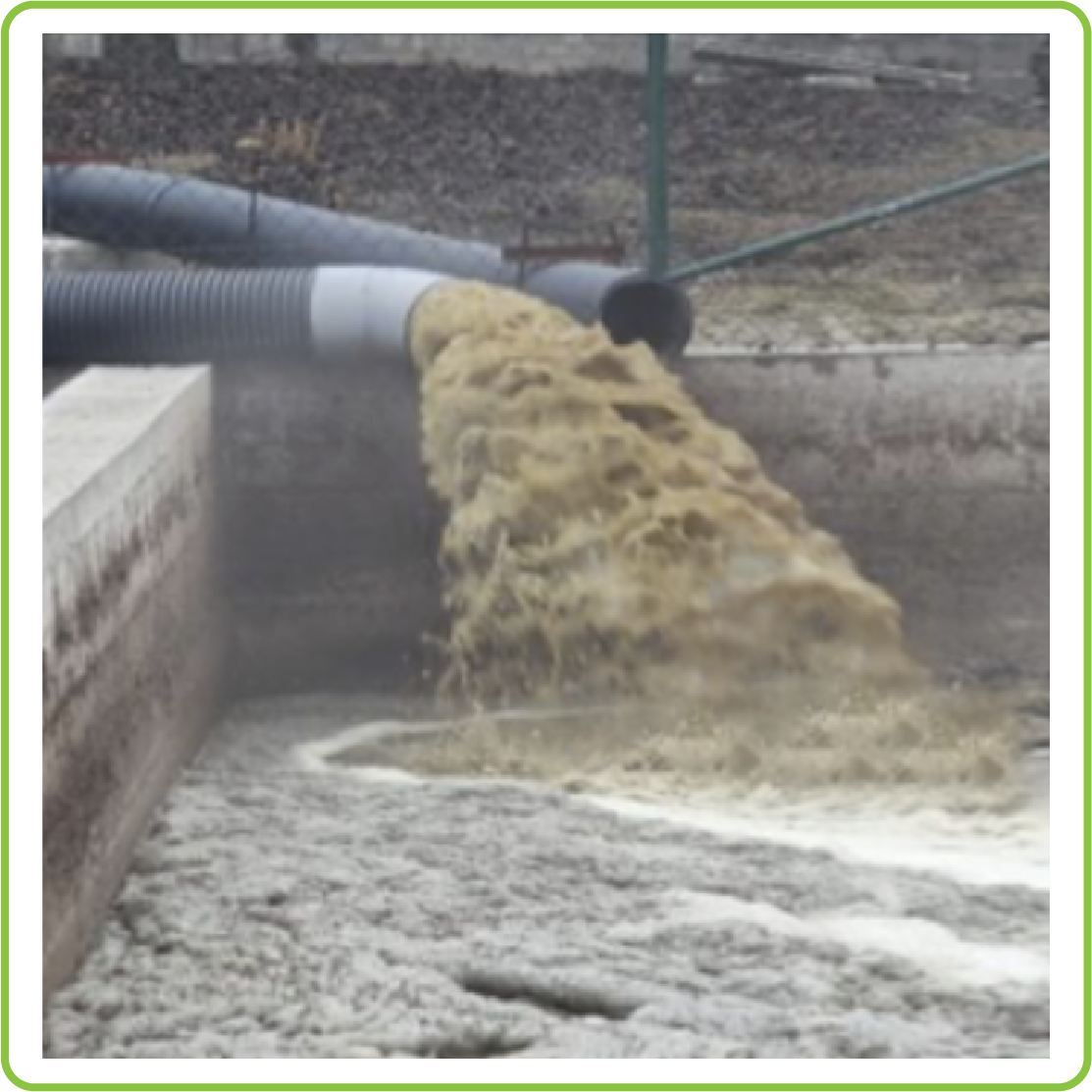
Developed in Catalonia to deal with water scarcity, NVZs & land availability, slurry contamination and to alleviate further ecological damage.
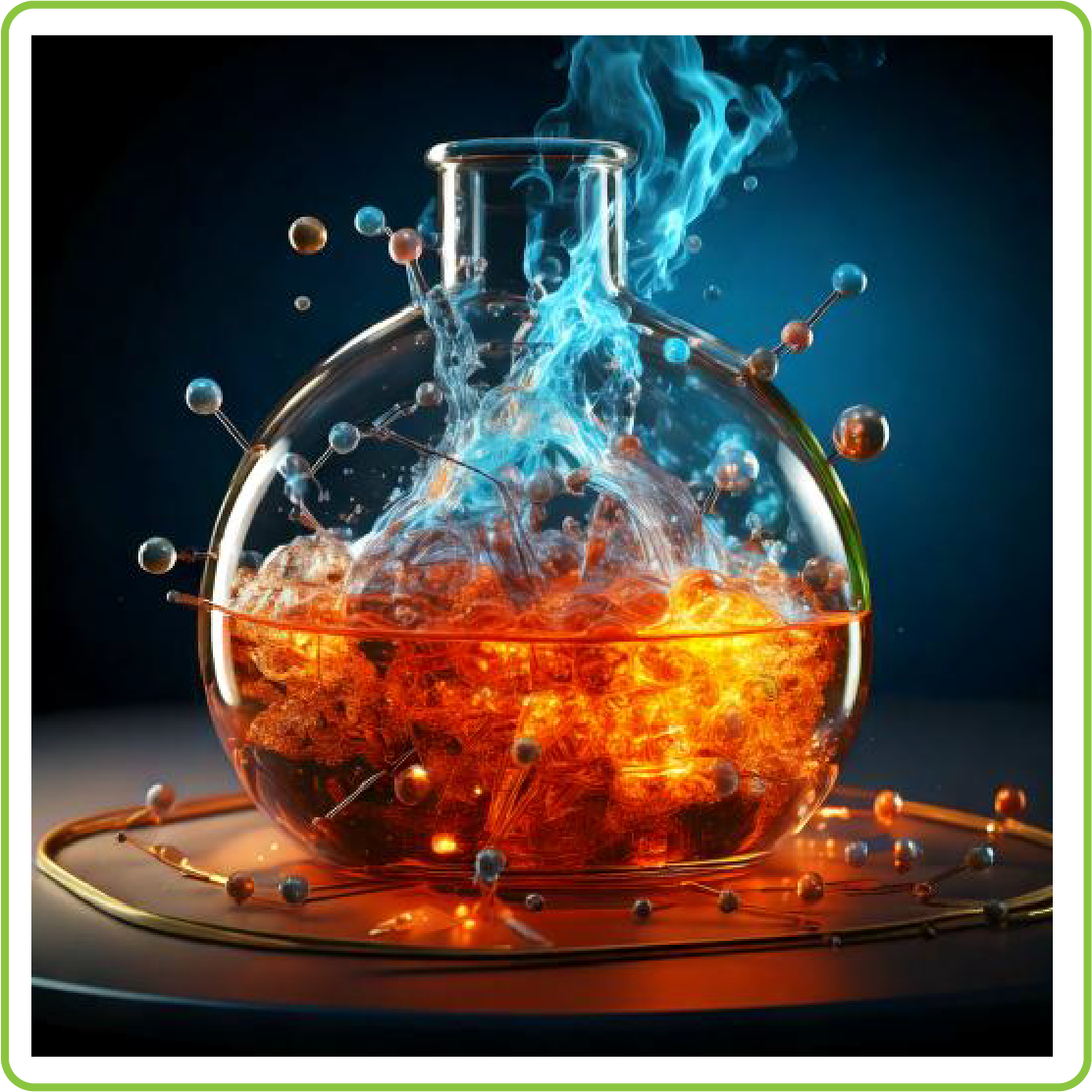
Advanced engineering combined with patented and proprietary physical/chemical innovation to reverse the bio-chemical reactions found in agri-food-bio-waste.
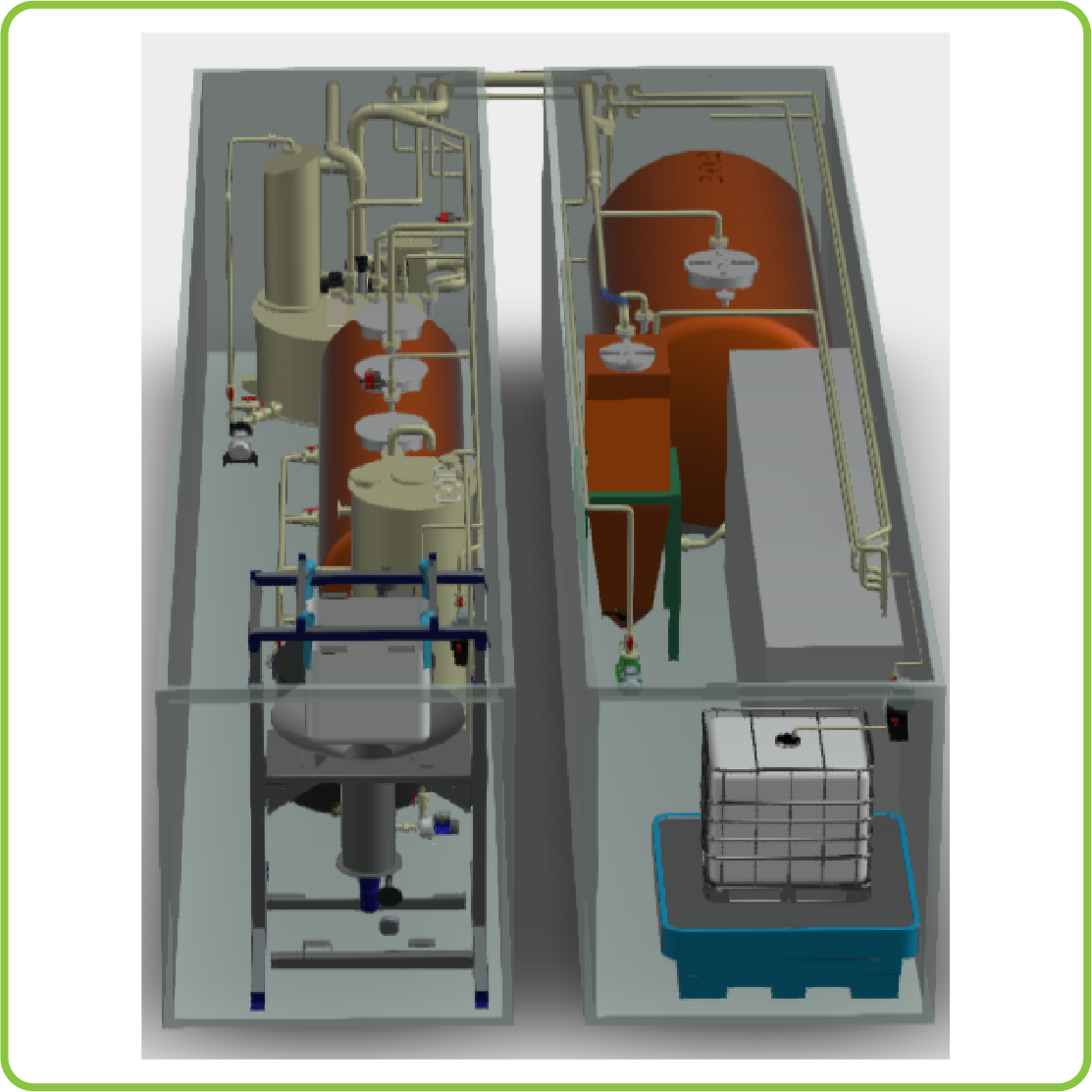
New modular flow technology is a customisable turnkey-ready treatment system, for volumes from 20m3/day, highly automated and monitored 24/7/365.
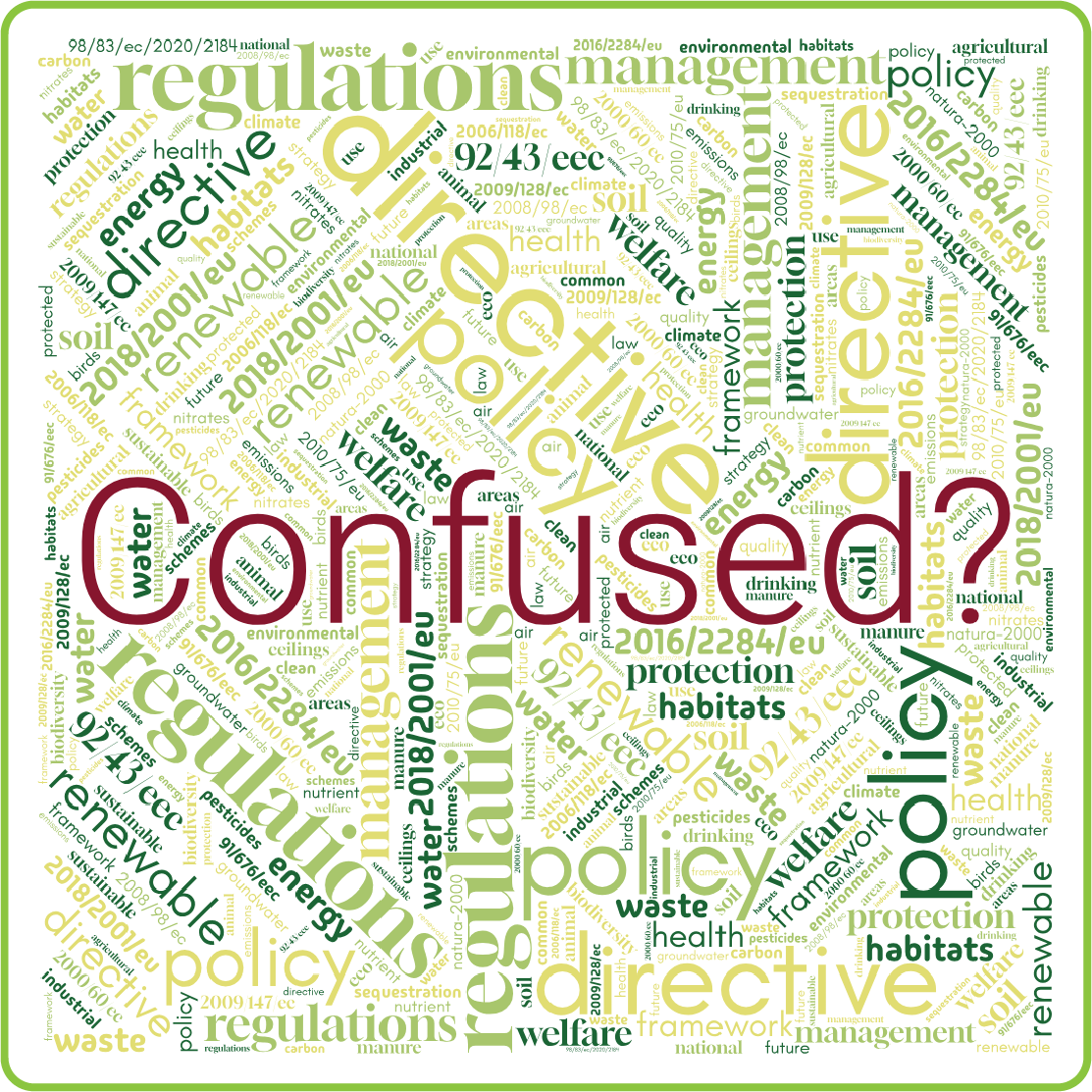
Compliant with the evolving EU Directives including Nitrates (91/676/EEC), Water (2000/60/EC), Groundwater 2006/118/EC + Green Deal ‘neutral by 2050’.
Sectors
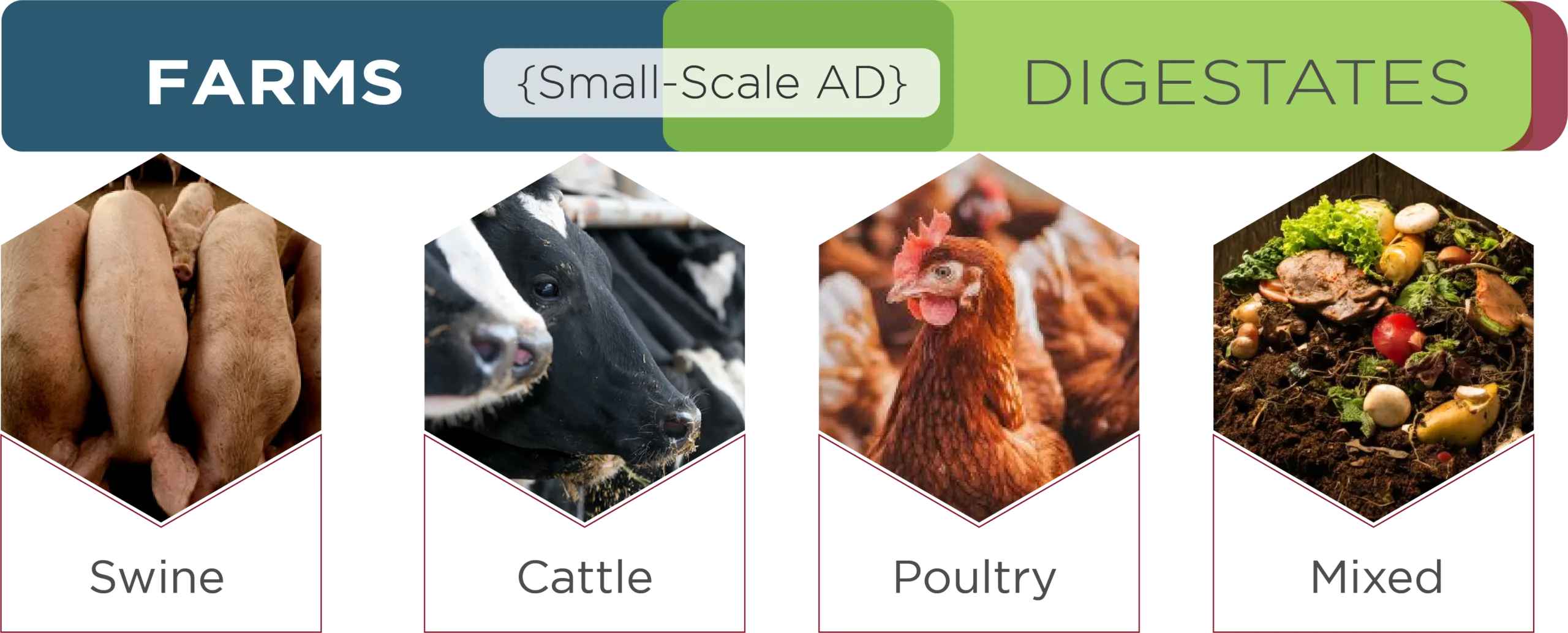
Focus: Helping farms improve their waste management and deliver a return on their investment. Our modular system can be integrated with existing facilities, in different configurations, making it flexible for both small compact spaces and larger farms. It also optimises the feedstock for small or large-scale anaerobic digester systems.

What goes in…

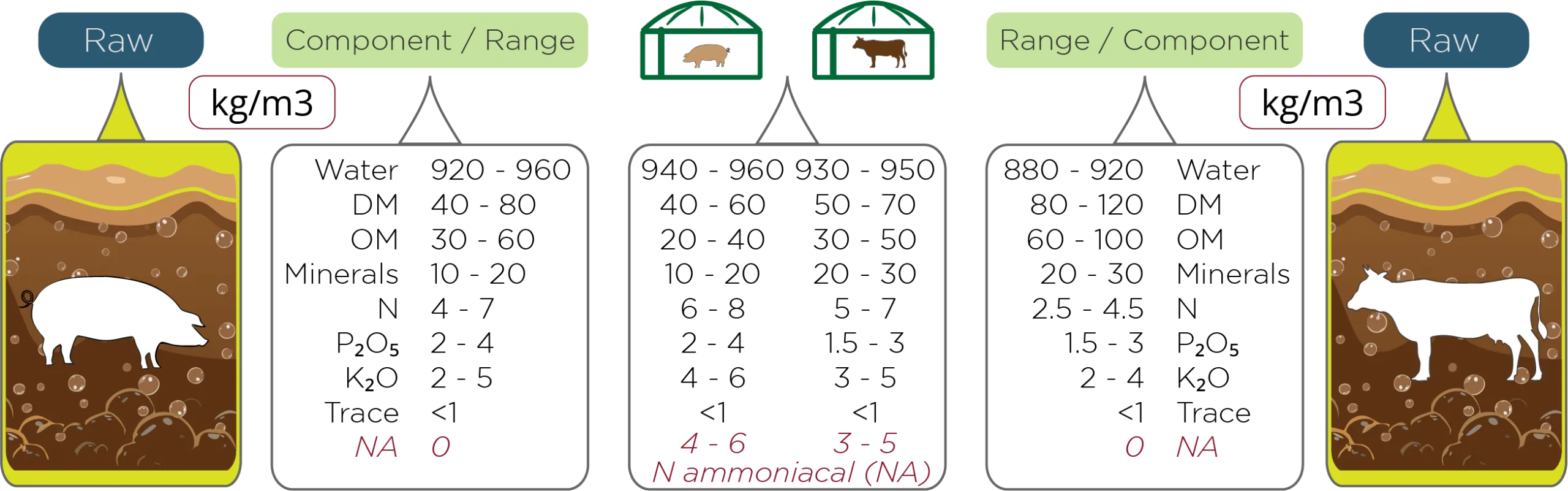
Pig
Water Content: Typically 92-96% of pig slurry is water.
Dry Matter (DM): Contains organic matter (fibrous material, fats, and proteins) and ash (minerals like calcium and magnesium).
Nutrients: Phosphorus and organic nitrogen) are generally concentrated in the solid fraction while potassium and soluble N,P are held in the liquid fraction
Anaerobic Digestion
Reduced Dry Matter: The digestion process reduces the dry matter (DM) content.
Higher Ammonium Nitrogen (NH₄⁺): Organic nitrogen is converted to ammonium nitrogen.
Phosphorus Concentration in Solids: Most phosphorus remains in the solid fraction.
Cattle
Water Content: Cow slurry is less liquid with a water content of 88-92%.
Dry Matter (DM): The higher dry matter content consists mainly of fibrous material from undigested feed and bedding, along with organic matter and some minerals.
Nutrients: Mostly organic nitrogen and phosphorus concentrates in the solid fraction, and potassium + ammonium nitrogen in the liquid fraction

…comes out

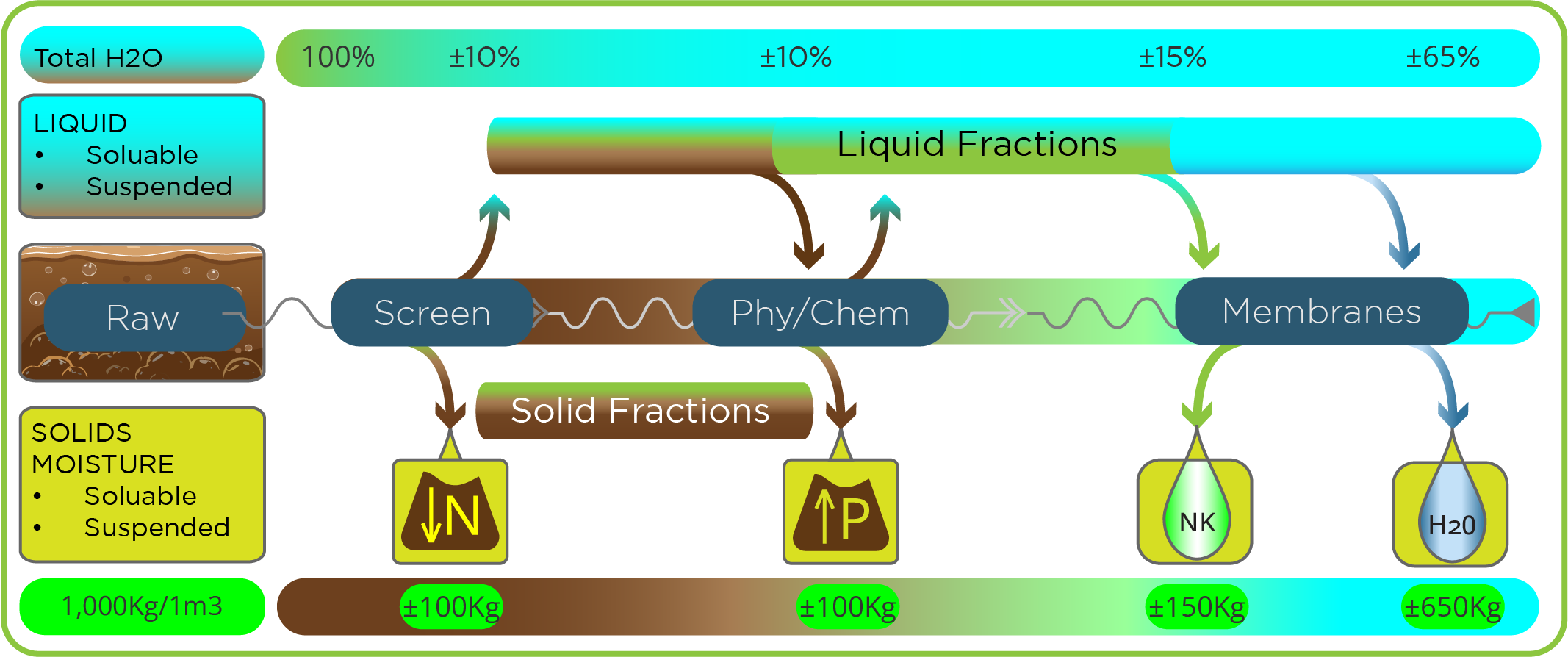
Seperation.
Raw slurry into solid and liquid fractions.
Solids and/or DM
Dry Matter
(includes Organic Matter/OM, moisture, carbon…).
DM↓N – Dry Matter with lower ammonium N
DM↑P – Dry Matter with higher Phosphorus
Bio-NK
Nutrient rich liquid & suitable for organic fertilizers from animal and plant origin
H2O – Clean – Permeate – Water.
Suitable for just about anything, except drinking.
2025 Continuous Flow Process
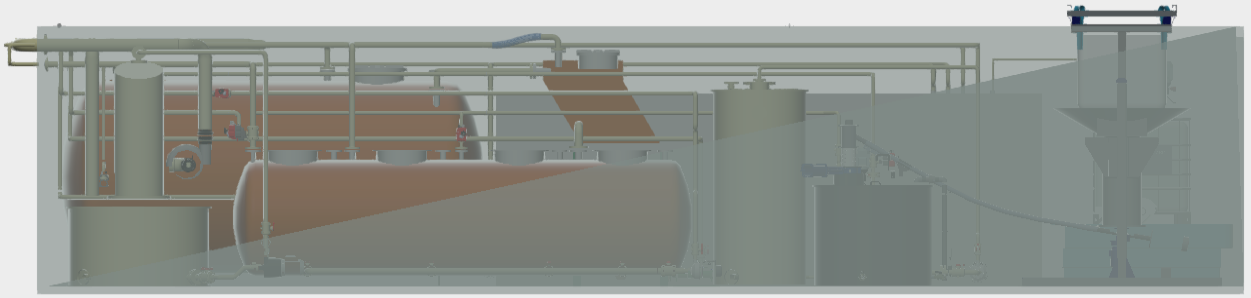
Our new continuous flow technology replaces the original batch system of ‘fill > treat > empty’ into a smooth, more effective and efficient process, with a reduced physical footprint and lower Opex costs.
► 4-bay reactor allows for improved coagulation periods and pH management, plus a reduction in the compounds required.
► Seperate flocculation minimises sludge build up in the system.
► Improved clarifier performance by maintaining a stead flow, enables more solids to be extracted.
► Reduced solids in the final liquid fraction means lower membrane costs: additives, operating pressures, clogging and replacement.

3 Cycles

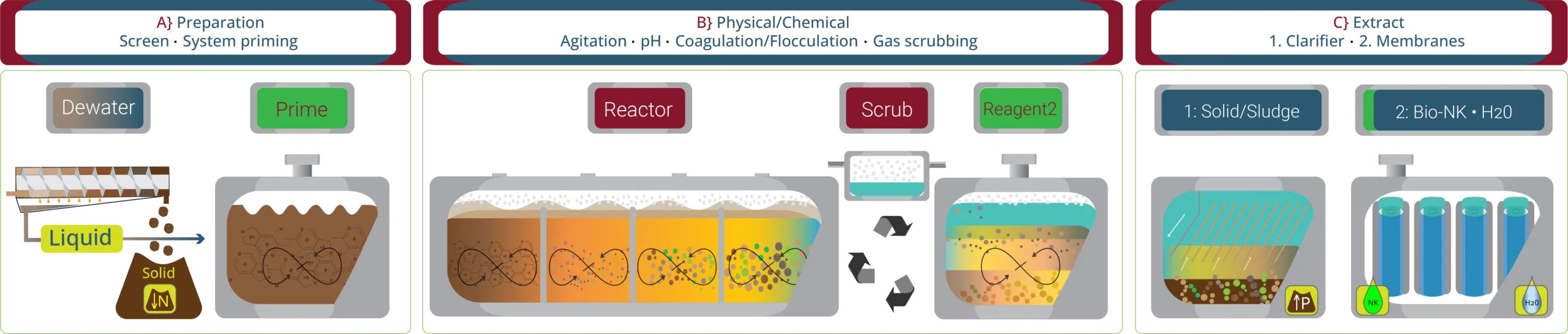
A. Mechanical separation.
Integrating existing on-site systems, the goal is to extract the liquid fraction at <150µ.
B. Physical Chemical.
Our proprietary technologies manipulate the chemical bonds through ph management, coagulation and flocculation to release solid and organic material, while gases are liquified and recycled through the system.
C. Extraction.
Clarifier removes solids while the liquid fraction flows to membranes to extract H20 & N,K bio-nutrient.
Maths
No two farms are the same, but in 2014, the team set out to find solutions to the very real challenges of water security, land use, slurry contamination and new ways to alleviate further ecological damage to our region.
From the initial R&D through testing, field trials, certification, commercialisation and installation, {nkaptur} offers a cost effective regulatory, environmental and operational solutions to those challenges.

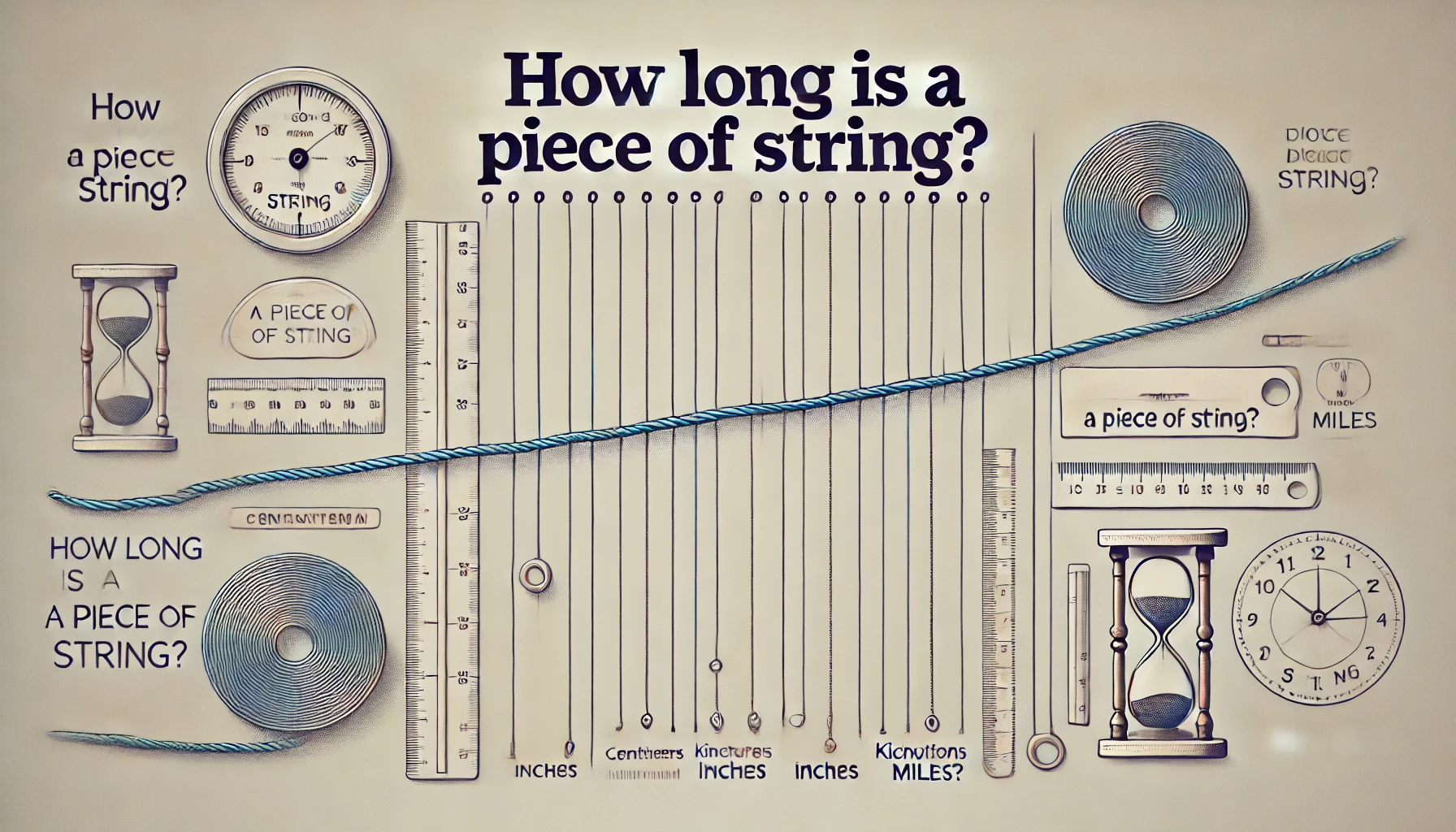
Investment ∙ Operation ∙ Timelines
From an efficient dewatering system to a full NRR & AD infrastructure, client need and specification drives the investment, operational costs and ROI of each project.
Contact us via our contact form or projects@nkaptur.com for more information on how our technologies can support a profitable move to ‘neutral by 2050’.
CAPEX Variables
Farm: slurry type, volumes, farm type, herd size, exisitng facilities, groundwork….
Technologies: with or without AD, fertigation or bio-fertilizer, water purity, crop needs….
Format: Single farm / local community cluster supporting multiple farms..
OPEX/m3 Variables
► Compounds & additives.
► Low power use (electricity).
► 365 monitoring.
► Limited human interaction.
► Scheduled servicing & maintenance.
Operational timeline: >25 years
With our monitoring, replacement and biannual maintenance service, {nkaptur} is engineered to function well passed the Green Deal deadline.

About {nkaptur}



{nkaptur} is a trading name of Pronespa. Pronespa is a privately owned chemical & industrial engineering company founded in 1981 and certified since 2002 as ISO 9001:2000/15 compliant quality management systems.
If you or your local community are interested in finding out more about our ‘neutral by 2050’ technologies, or you’d just like to receive occasional updates (don’t worry, we don’t like spam either), please complete our contact form.
Foot note: why nkaptur? The idea around the word ‘encapture’~ to ‘capture within’ /enˈkæp.tʃər/ ~ ‘c’ & ‘k’ have similar sounds and N, K, P are our target nutrients, the { } implying within ~ but mainly because the .com domain was available.